process
Project
management
Engineering
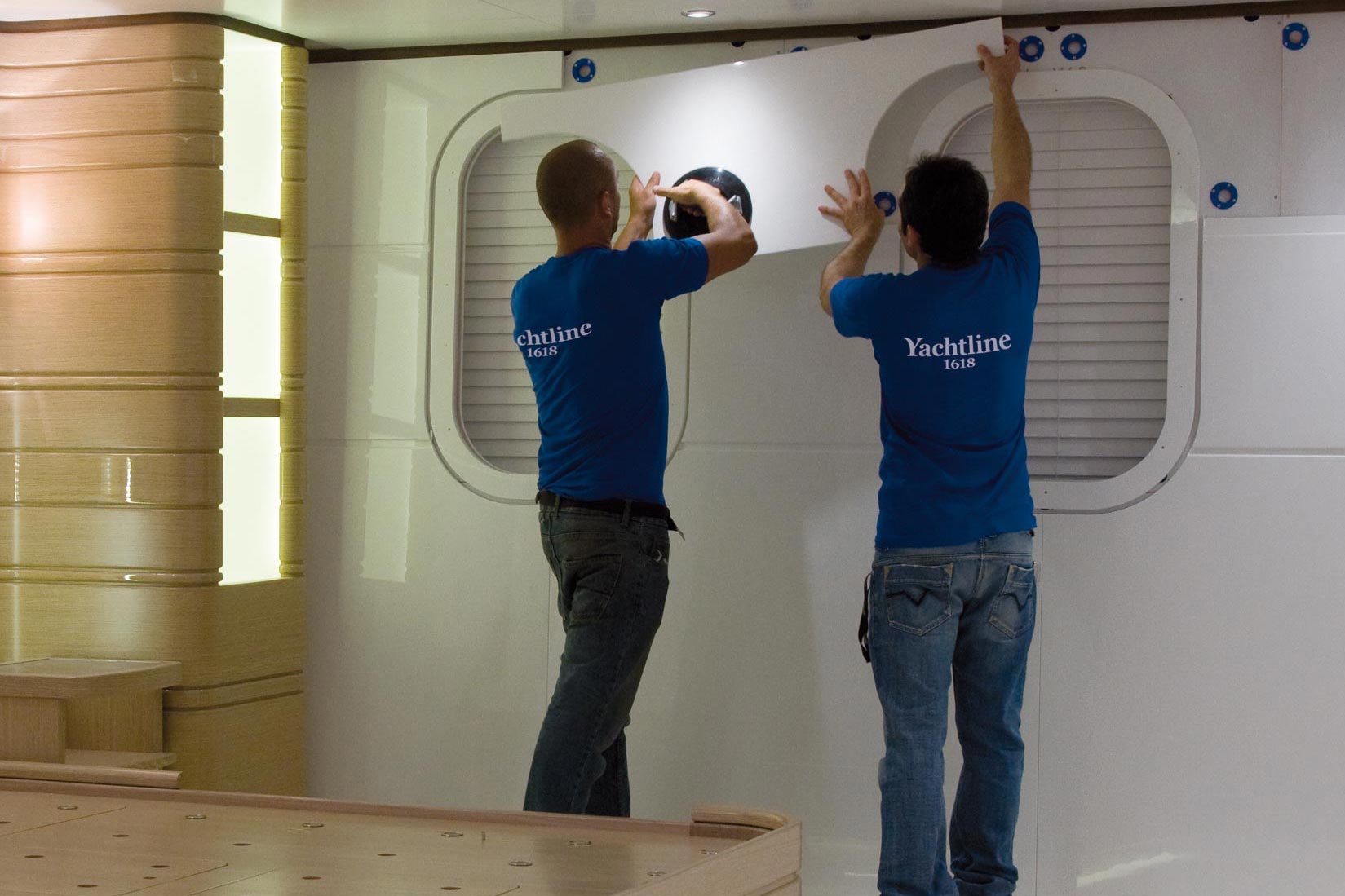
Partitioning
The net space is outlined by CNC cut templates which the volumes of the furniture and of the systems: Information which will be necessary during the construction of the boat and which will be a guidance to the workforce on board.
Meantime, a copy of the template is used in the mock-up areas for proceeding with construction of the furnishings, at the same time as progress on board, optimising the final delivery times.
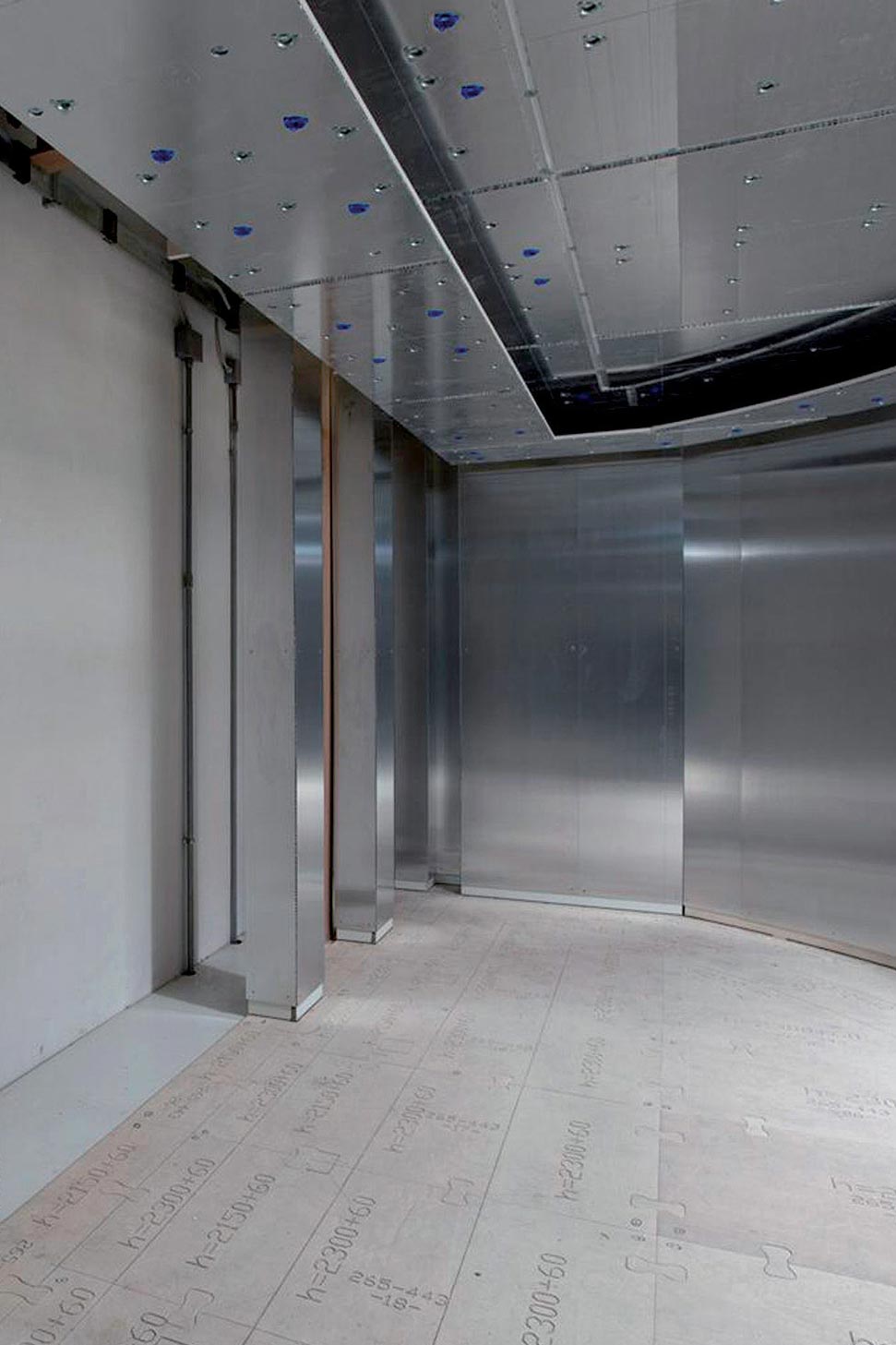
Production
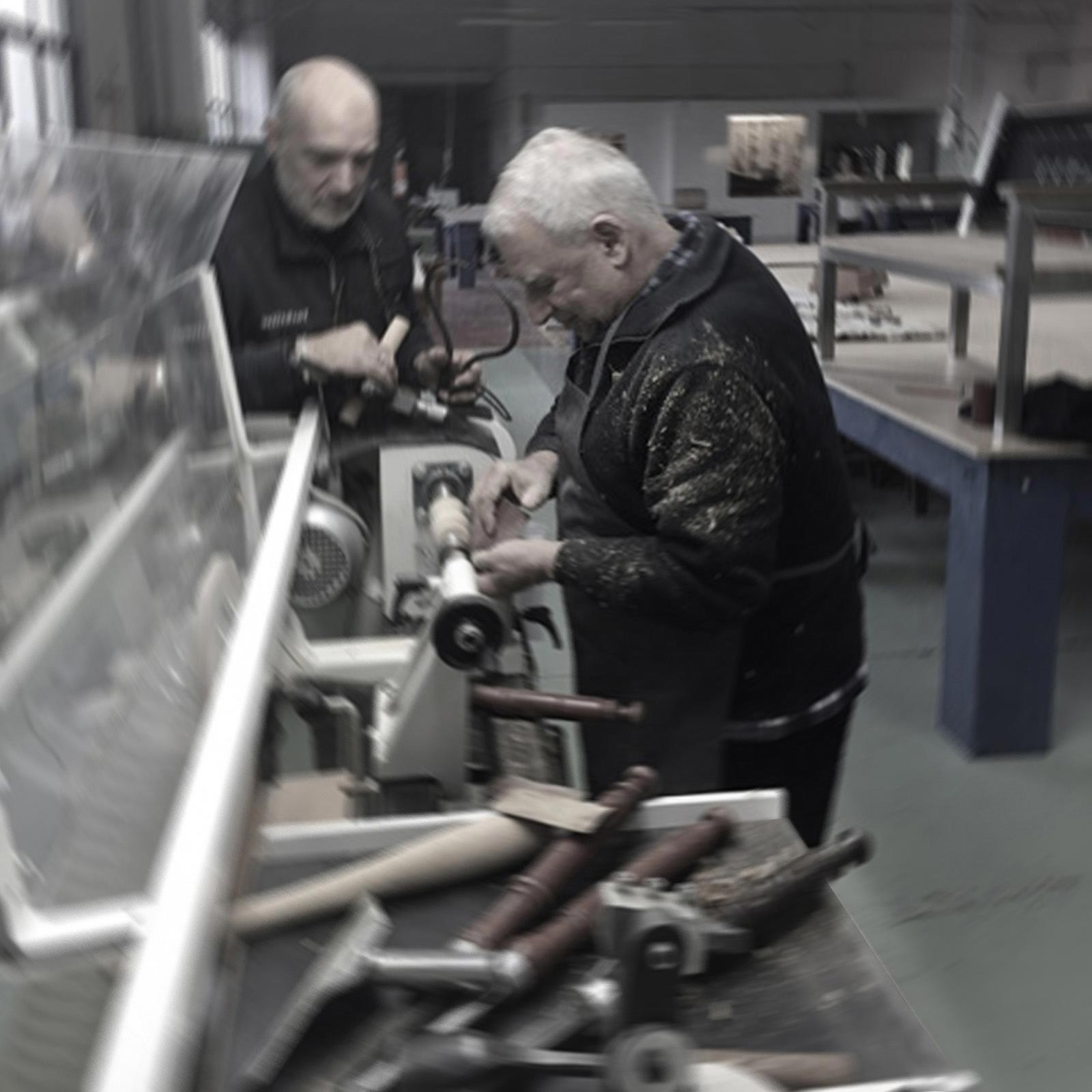
Yet, it is the hands of the craftsman who get to the heart of the project.
The secrets of burl and wood have deep roots: from observing the tree down to the studying the veins, the reflections and the chromatic effects.
Everything is looked after down to the smallest detail.
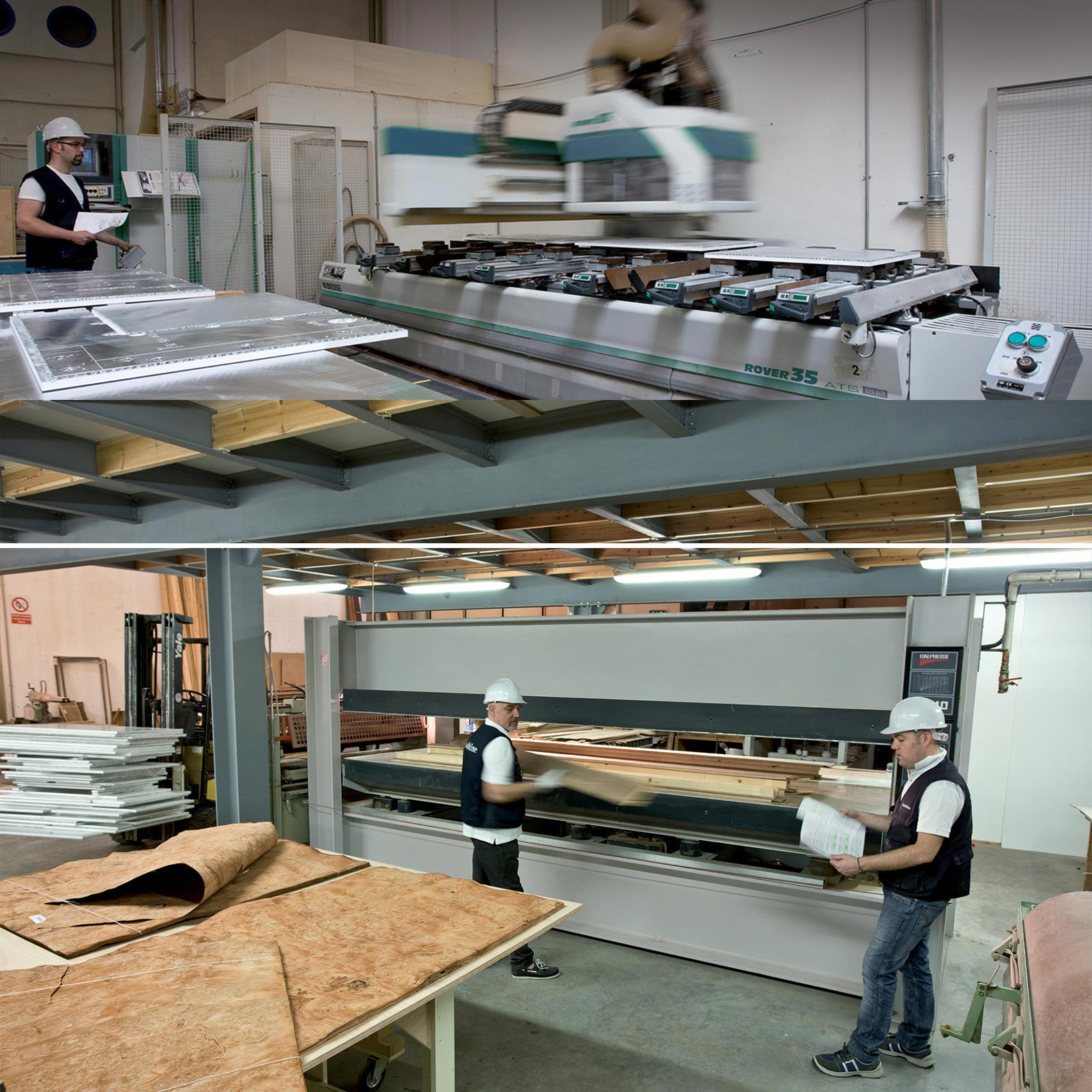
What is apparently invisible, for us represents the exclusivity and the luxury of an interior.
Mock-up
This production procedure, enforced for all areas and in all their components, allows to check the furniture together with the Client’s technicians reaching a fully satisfactory completion of the work, in compliance with contractual times and budgets.
Finishing
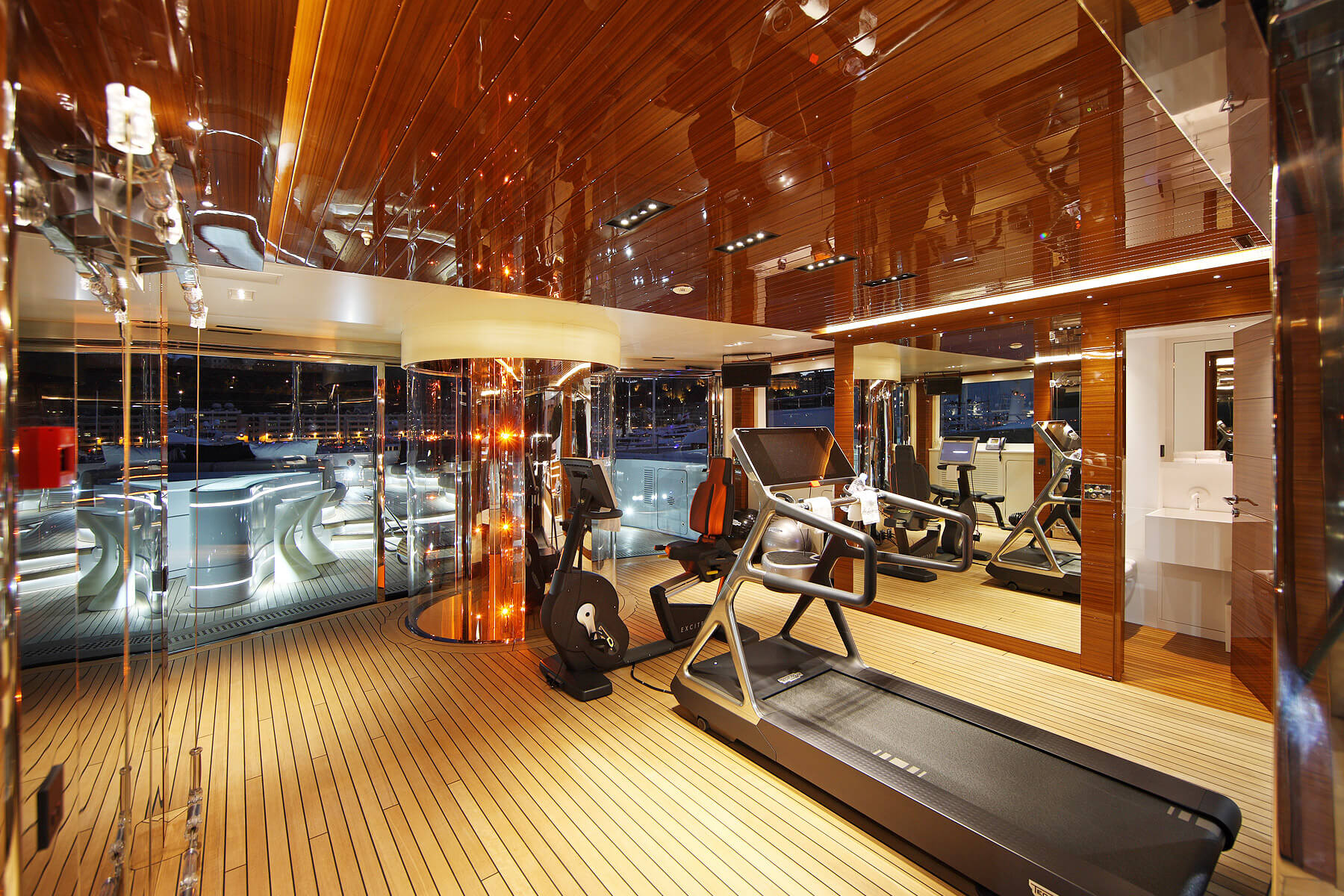
The coating, lacquering, sanding and polishing booths are of the latest generation and lead to excellent results.
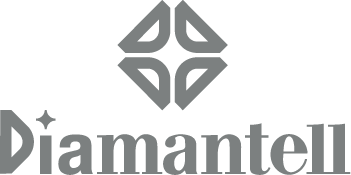
Fitting on board
The fitters are carefully selected and trained, they operate under the careful supervision of our managers and they are masters in solving the inevitable situations which arise on board, given the articulated and complex construction process which involves the yard and the system’s technicians.
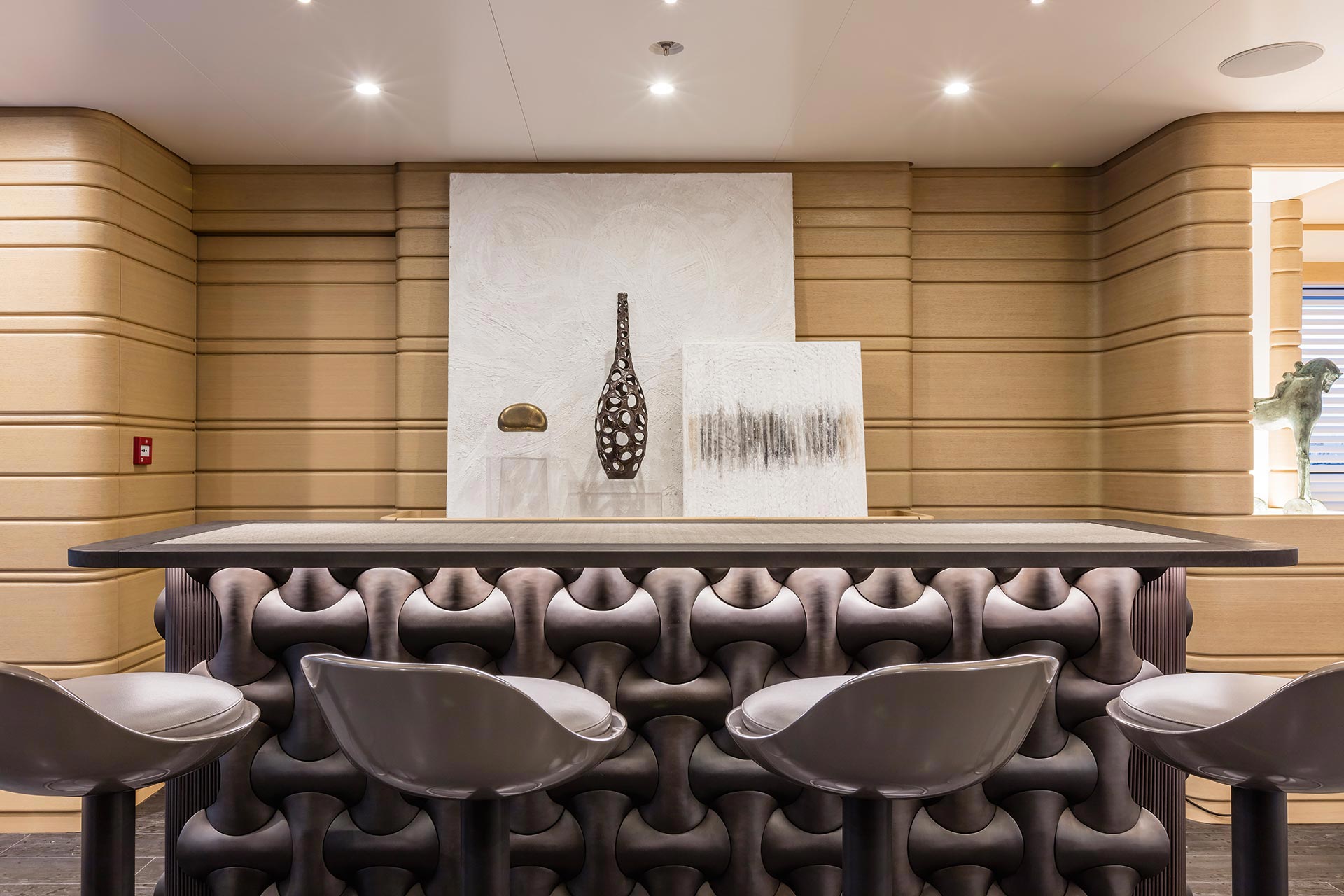
Delivery

In this regard Yachtline 1618 developed a customized production system with a unique organization.
The “QR Code” of each individual component allows to make more efficient the fitting, to manage the thousands of components and, whenever it should be necessary, to minimize each on-board intervention throughout the life of the yacht.